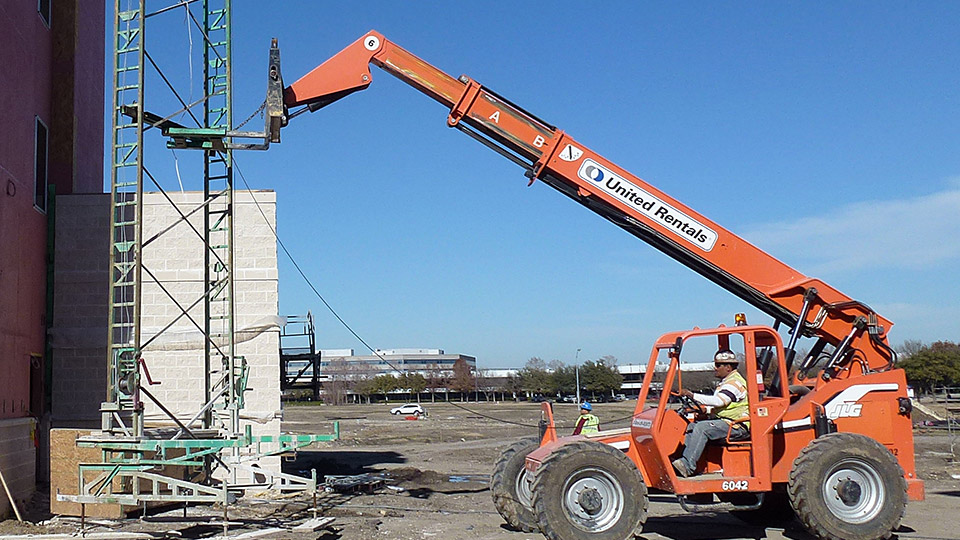
The Swivel Forklift Bar allows your lift driver to grab towers from one wall and land them at the next wall in minutes, and at any angle. Notice the mud sills are nailed to the leveling jacks.
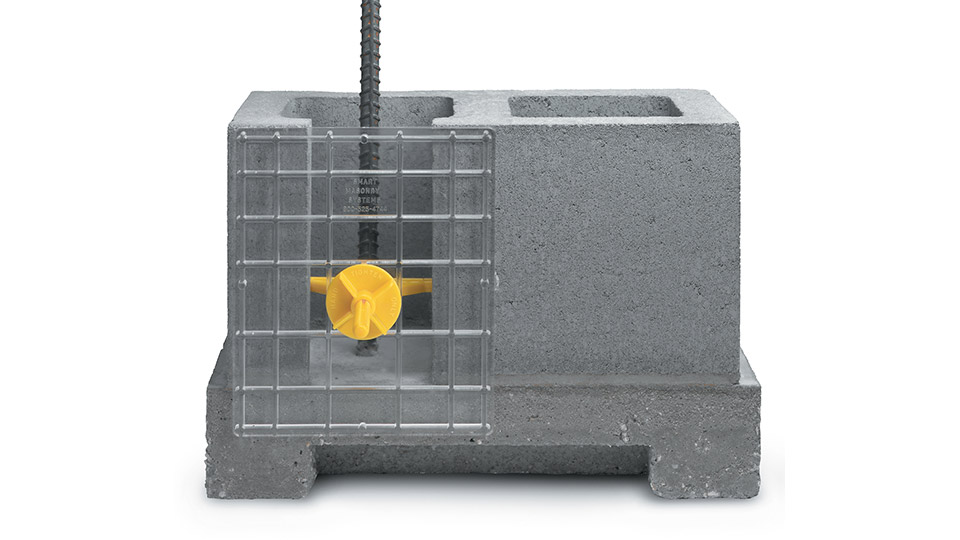
The transparent window allows inspection of the cell, both before and after the pour. The manufacturer says he’s never had a compliant about a blowout.
To grout in 12-foot, eight-inch lifts, there are three conditions that are easy to meet: 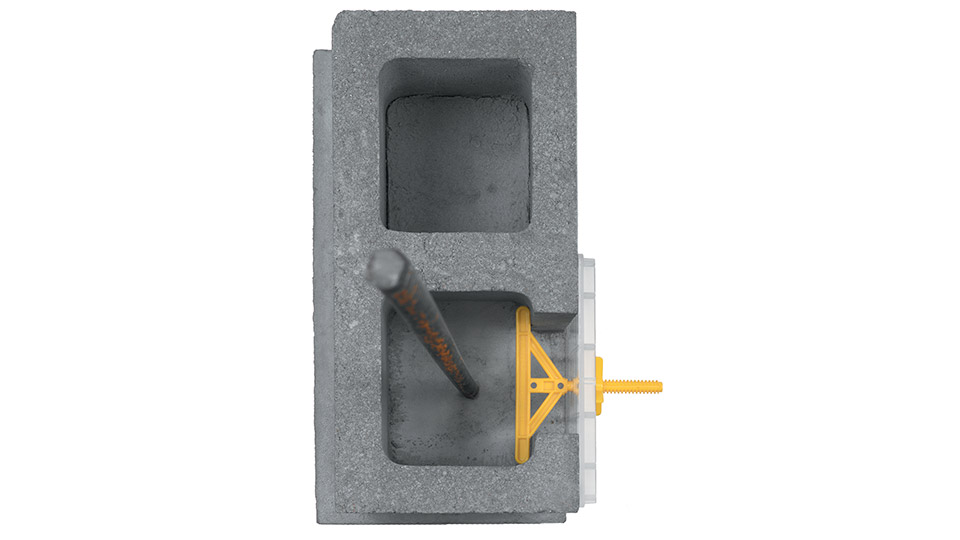
A T-bolt holds the plastic window flush with the face of the wall. After the pour, the window is removed, and the T-bolt is snapped off.
You will need a clean out at the bottom of each cell. That’s what usually stops most people cold. Clean outs are a big pain in the behind, and often blow out, until now. A retired mason contractor, Randy Jensen, invented and manufactures the Smart Masonry System, a transparent plastic window (see Photo 3) that covers a clean out opening. It goes in place in literally a minute, allowing you to pour immediately after inspection. Randy says it will not blow out and leaves the grout flush with the surface of the block (see Photo 4) — huge improvement over nailing a piece of plywood to the wall (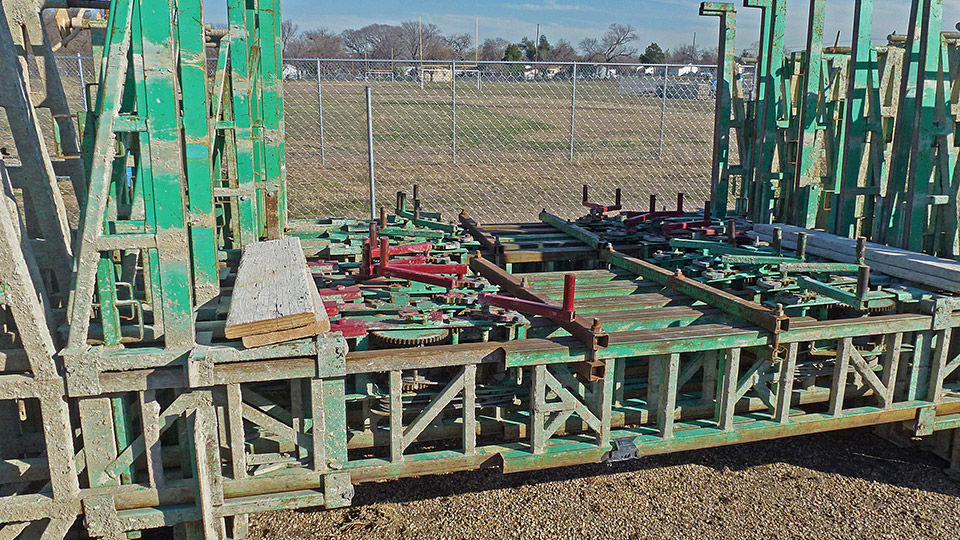
This contractor clamps his base towers together in packages of 10. Each one is four feet wide, allowing him to put two packs across his trailer. Each pack is 14 feet long.
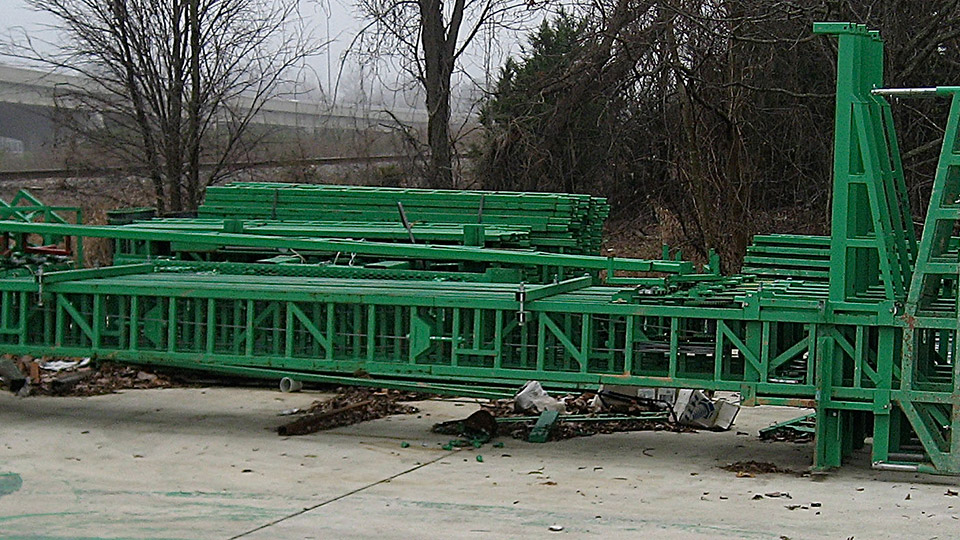
Base Towers with extension towers attached are clamped together in four-foot-wide 10 packs. Many Non-Stop users leave their towers completely assembled 18 or 27 feet high and never take them apart.
In my research talking with contractors, I gathered more tips than I can include in one article. I’ll put another article together containing the best nuggets I gathered. If you have a tip you’d like to share, please email it to me at my email address below.